Ceramic foam structure has demonstrated high performance in the field of combustion burners beacause of its superior properties including good thermal shock resistance, thermal conductivity and high surface area. Standard Ceramic is one of the first pioneers in the research and development of SiC foam.
We actively collaborate with partners across the energy, metal foundry and areospace industries to develop the next generation energy efficienct low emission burner.
70%
High burning efficiency
NOx and CO pollutant reduction up to 70%
50%
Higher TMax
Up to 50% more efficienct
comparing to traditional method
x10
Burner/ heat exchanger
size reduction up to 10 times
Fast heat dispersion
High combustion efficiency
Its large porosity, and extensive specific surface area results in its strong heat storage capacity. Heat radiation, convection, and conduction, all three heat exchange methods simultaneously spread heat evenly across the combustion zone, therefore maintaining a stable and homogeneous temperature gradient.
3D Network
Foamed Silicon Carbide (SiC) material has three-dimensional interconnected network structure, which creats large specific surface and high permeability. In combination of its high specific strength, our specially designed SiC foam can enhance the combustion efficiency by 50%.
SiC Foam Matrix
High Temperature Resistance
No meltdown during high heat up to 1600° C
High Porosity
Customizable porosity
Maximized burning efficiency
Thermal Conductivity
Highly heat conductive
Homogeneous heat distribution
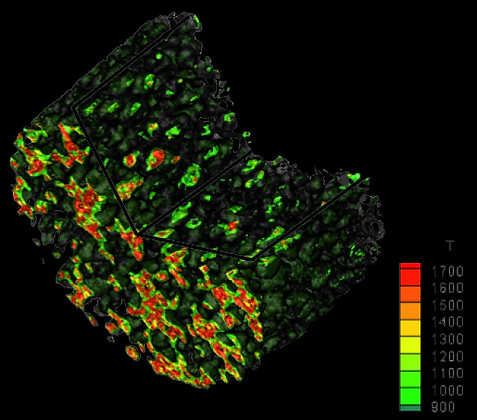
Open Flame vs
Porous Media Combustion (PMC)

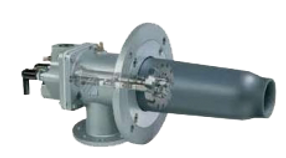
2MW/m2
1:6 max.
Uneven
Low
30%
1~30 MW/m2
>>1:20
Even
High
80~90%
Power Density
Range
Temperature Homogenity
Customizability
Radiant Efficiency
Porous Media Material
Techinical Comparison
Unit
g/cm3
W/(m*K)
W/(m*K)
J/(g*K)
-
℃
-
Density
Thermal Conductivity (25℃)
Thermal Conductivity (1,000℃)
Specific Heat
Radiation Coefficient (1,200℃)
TMax
Thermal Shock Resistance
SiC
3.2
120~140
30 - 80
0.7 - 0.8
0.85 - 0.95
1,600
very
good
Al2O3
3.75
20 - 40
5 - 6
0.9 - 1.0
0.28
1,600
poor
ZrO2
5.56
2 - 5
2 - 4
0.5 - 0.6
0.3
1,600
good
FeCrAlY
7.4
15 - 17
-
0.7 - 0.8
0.5 - 0.6
<1,100
very
good
Ni
8.89
80 - 88
-
0.75 - 0.85
0.3 - 0.5
<1,100
very
good
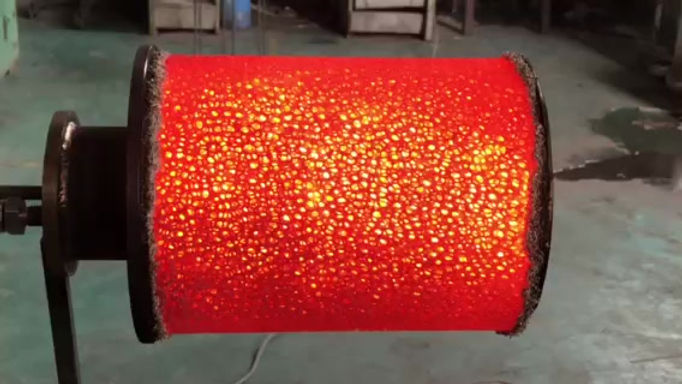
The 3rd Generation
Porous Media Combustion
Our latest PMC SiC foam is compatible with the 3rd generation gas combustion technology, and can reach higher Max temperature comparing to the 1st generation conventional gas combustion technology and the 2nd generation heat storage combustion technology.
The 3rd generation PMC SiC foam, under the same conditions, achieves the highest panel temperature 100 °C higher than the 2nd generation burner, and nearly 200 °C higher than the 1st generation burner.

1st Gen.
PMC Burner
2nd Gen.
PMC Burner
3nd Gen.
PMC Burner
The heat radiation rate per unit area is also higher. Under the same panel conditions, the burning power is 80% higher than the 2nd generation burner, and is more than double that of the 1st generation burner.
From the experimental results, the 3rd generation PMC burner has obvious performance advantages, the temperature of the panel peaks at 1,370 °C, and maintains stable combustion, this is especially suitable for situations that demands rapid radiant heating.

Customization
Porosity and Pore Size
Customizable pore size and volume fraction. Minimized blind hole, the solid phase volume fraction can be precisely controlled during manufacturing.

1mm
Diameter
3mm
Diameter
4mm
Diameter
2mm
Diameter
Size and Machinability

Precise machining is possible thanks to the high strength of SiC material. Our low deformation sintering technology maintains fine pore structure while keeping the module assembly structure, the result is the material’s excellent heat absorbing capability.

Hexagonal and quadrilateral foam SiC ceramic foam with various pore structure can be customized upon request. Flexible modular design is also available, which can be used for large surface construction.
Application
Case Study

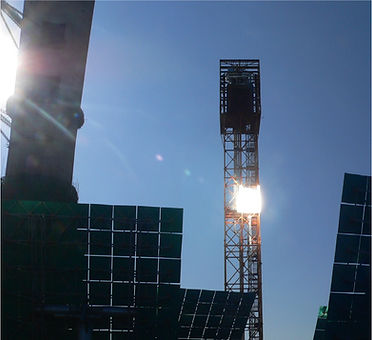
1MW Solar Heat Exchanger assembly
at Yanqing Solar Farm, with surface area of 2.167m2
